Navigating Product Regulations and Standards
- Lucas Gabriel
- Oct 21, 2024
- 7 min read
Updated: Nov 16, 2024
A summary of the regulatory demands, encompassing safety standards, packaging, labelling and compliance.
by Lucas Gabriel ©2019

Ensuring compliance with product regulations is critical to bringing FMCG (Fast-Moving Consumer Goods) to market. Different regions have distinct regulatory requirements, and navigating these can be challenging, especially when dealing with both international and local standards. Here's an overview of the key considerations and strategies to ensure compliance.
Understanding Regulatory Product Requirements
Each country has its own regulations, mainly designed for the good of its people and government objectives. They primarily cover safety, labelling and environmental compliance. Understanding both global and local regulations is essential when buying, selling, importing, exporting or developing products.
It's important to note that International and Local regulations do not supersede one another. In my experience, it is best to satisfy both or whatever is more stringent. In many instances, they are each closely aligned; however, there are nuances for each country or federation—some more than others.
Global/International Safety Standards
Examples of various international standards to govern the safety and sustainability of consumer products:
ISO (International Organisation for Standardisation) standards apply to quality and environmental management. ISO standards are globally agreed-upon best practices developed by experts to improve various aspects of business and operations. They act as formulas for optimal ways of creating products, managing processes, delivering services, and sourcing materials based on input from manufacturers, buyers, users, and regulators.
ISO standards cover:
Quality management: Enhancing efficiency and reducing product failures.
Environmental management: Minimising environmental impact and promoting sustainability.
Health and safety: Reducing workplace accidents.
Energy management: Lowering energy consumption.
Food safety: Preventing contamination.
IT security: Securing sensitive information.
These standards help address both well-established needs and emerging global challenges.
ASTM (Advancing Standards, Transforming Markets) International provides over 12,000 standards globally and is commonly referenced in the U.S.
EN71 is the European toy safety standard, including mechanical, chemical, and flammability safety requirements.
RoHS (Restriction of Hazardous Substances Directive) restricts hazardous substances in electrical and electronic products. It is an EU directive restricting specific dangerous materials in electronics and electrical products and is applicable to products sold in the EU that must meet compliance standards for six restricted substances.

When manufacturing for international markets, ensure your products adhere to the relevant standards to avoid compliance issues. Adhering to standards and selling products internationally requires a lot of planning, investigation and testing. At the very least, it often means additional design considerations for packaging and instructions.
Summary of Australian Product Safety Standards
Australia has stringent consumer protection regulations, the Australian Competition and Consumer Commission (ACCC) oversees product standards.
Mandatory vs. Voluntary Standards
Mandatory Standards: Compulsory requirements for certain products to ensure safety and information accuracy before sale. Supplying products in Australia that do not meet these standards is illegal.
Voluntary Standards: Non-compulsory guidelines ensuring product reliability, safety, and performance. While not legally required, the Government can partially or fully adopt these if safety risks exist.
Pro Tip: Many regulations can be interpreted differently. Depending on organisational objectives (cost and market) and product or industry experience, avoid potential risks by implementing and adhering to mandatory standards where-ever possible. It may help create a better quality product with a higher value proposition.
Key Areas for Mandatory Standards Compliance
Safety Standards: To prevent injuries and address risks by setting minimum requirements on performance, materials, design, construction, labelling, and more.
Information Standards: Ensure consumers receive critical information (e.g., ingredient labelling on cosmetics or care instructions for textiles) to make informed purchasing decisions—these commonly impact packaging, labelling, instructions and advertising.
Compliance Requirements
Suppliers, including manufacturers, importers, and retailers, must ensure products meet relevant mandatory standards.
Under Australian law, "Supply" includes any resale, lease, hire, or transfer of goods or services.
Consequences of Non-Compliance
Legal penalties, fines, and business impacts include product recalls, redesign costs, and potential damage to reputation.
Unsafe products risk causing serious injuries or death, particularly among children, resulting in significant legal, financial and social costs.
Be sure of your obligations, especially if selling in international markets.
Developing New Mandatory Standards
The Australian Government conducts research, market analysis, and consultations before introducing new mandatory standards, considering regulatory and non-regulatory impacts.
Implications for Business and Community
Ensuring product safety avoids legal repercussions, protects public health, reduces healthcare costs, and maintains consumer confidence in the market.
Pro Tip: Partnering with local market regulatory experts, testing labs and industry advisory groups can help you stay informed and compliant with changing regulations and avoid costly mistakes.
Key Areas of Compliance
To meet regulatory requirements and ensure market entry success, focus on the following key areas:
Safety Testing and Certifications Testing products for compliance with safety standards is essential. This includes checking for choking hazards (small parts), sharp edges, strength (pull) tests and toxic materials for toys. FMCG products should undergo testing for contaminants, shelf-life stability, and ingredient safety. Testing Labs of agents will conduct tests specific to your product, market and industry.
Pro Tip: Engage with a local certified testing lab that specialises in your product category to conduct the necessary tests and certifications. This is your best option from a number of standpoints in a business context including risk mitigation. The testing, reporting and certification process will often require "final samples", that you should not expect to be returned.

Labelling and Packaging Requirements Regulations often specify how products should be labelled, including language, font sizes and information that must be displayed, such as:
Age Appropriateness (for toys): Clearly indicate suitable age ranges.
Ingredient and Material Lists: List all ingredients, including allergens.
Safety Warnings: Display relevant warnings, e.g., "small parts - choking hazard."
Country of origin: Certain markets require information about where the product was made.
Non-compliant labelling can sometimes result in delays, destruction and/or fines.
Chemical and Material Restrictions Be aware of restrictions on certain chemicals and materials, such as lead content in paint for toys or preservatives in food. These restrictions vary by market and can impact your choice of materials and production processes.
Navigating Customs and Quarantine in Australia
Australia's quarantine regulations aim to protect the country from risks. When importing, ensure you meet the following requirements:
Customs Declaration and Documentation: Ensure all paperwork is correctly filled out, including the Import Declaration, which provides information about the goods, their value and their origin.
Biosecurity Requirements: Government Authorities may inspect products, especially if they contain organic materials. For example Toys with wooden parts or natural fibres, for example, may need destruction, treatment or fumigation. These costs are then passed to the owner or responsible parties.
Taxes, Tariffs and Duties: Calculate applicable costs before pre-sales, production and shipping, as these can drastically affect the overall viability. Check if your products are eligible for subsidies or preferential tariffs under free trade agreements.
Leveraging Third-Party Providers for Compliance
As best practice, consider engaging third-party providers to assist with regulatory compliance. These are your best defence in risk mitigation:
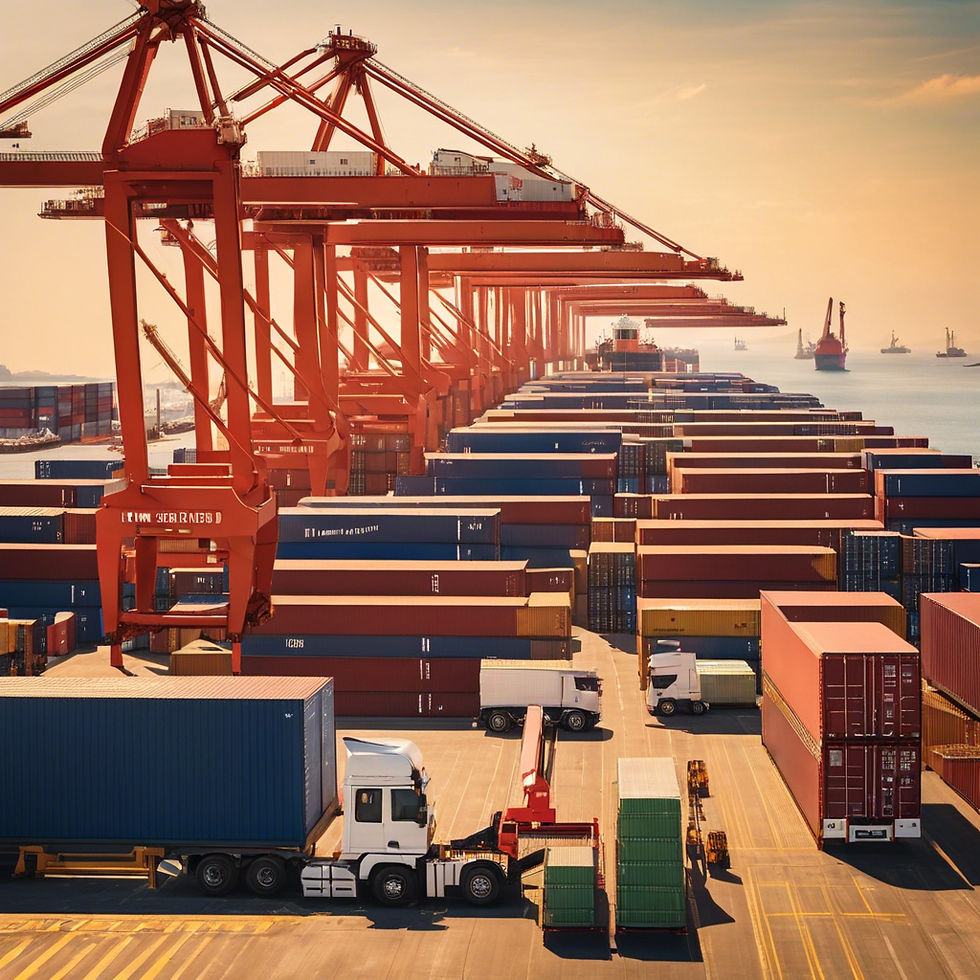
Customs Brokers: Help ensure all documentation is correct and expedite the customs clearance process.
Testing and Certification Agencies: Offer product testing and certification services to meet safety standards.
Industry Consultants and Associations: Provide timely and updated advice on meeting compliance requirements across different markets and industries. Associations have numerous added benefits. They can offer product or industry advocacy, professional network development, professional services, and industry events. Associations can also provide wider advice and insight into your market, helping you analyse trends, competitors, opportunities and risks.
Establishing a Compliance Framework for Your Business
To streamline the process of regulatory compliance, set up a structured framework within your business- provide the support and resources it needs:
Internal Compliance Team Establish a team dedicated to monitoring regulations, working with suppliers, and ensuring all products meet necessary standards. This can often be aligned with Q&A and Governance.
Regular Training Train staff on compliance requirements for different products, industries and markets to reduce non-compliance risk.
Supplier/Vendor Audits Conduct regular audits of your suppliers to ensure they adhere to the necessary quality and safety standards.
Continuous Monitoring Keep track of regulatory changes impacting your products and adjust your compliance processes accordingly.
General Compliance and Standards
ISO Standards: The International Organisation for Standardisation (ISO) sets a range of standards to ensure quality management, environmental responsibility, information security, and more. For example, ISO 9001 focuses on quality management systems, while ISO 14001 is centred on environmental management practices.
FSC (Forest Stewardship Council): A certification for wood, pulp, and paper products that confirms they come from sustainably managed forests. Companies often use this accreditation for packaging or any materials derived from wood to demonstrate environmental responsibility.
CE Marking: In Europe, CE marking indicates that a product complies with relevant EU safety, health, or environmental requirements, especially for electrical and electronic items.
RoHS Compliance: Restriction of Hazardous Substances (RoHS) applies to electrical and electronic equipment, limiting the use of specific hazardous materials like lead and mercury.
Australian Standards: AS/NZS standards provide specific requirements for various products in Australia and New Zealand, ensuring compliance with local regulations and quality expectations.
Digital Products
While physical products are often subject to specific regulatory requirements, digital products must also adhere to certain standards, particularly concerning data security, user experience, and accessibility:
WCAG (Web Content Accessibility Guidelines): These guidelines ensure digital content is accessible to people with disabilities. Compliance with WCAG is becoming a legal requirement in many jurisdictions, including Australia.
ISO/IEC 27001: A standard for information security management systems, essential for organisations that handle sensitive data or develop software.
GDPR (General Data Protection Regulation): While primarily a European Union regulation, GDPR affects any digital product that collects or processes data from EU citizens, enforcing strict data privacy requirements.
Open Data Standards: These help ensure data interoperability and accessibility, particularly in digital twin projects or smart city initiatives.
Accreditations for Digital and Technology Products
TISAX (Trusted Information Security Assessment Exchange): This exchange is specific to the automotive industry and ensures that companies meet information security standards.
ISO/IEC 12207: Addresses software lifecycle processes, setting out requirements for the acquisition, supply, development, operation, and maintenance of software products.
Awareness of these standards and incorporation into your processes can significantly enhance your product's credibility, access to products, and sustainability credentials.
Navigating product regulations, whether global or Australian, is a crucial step in ensuring successful development, importation and sale.
By understanding key standards specific to your products, customs processes and compliance strategies, businesses can minimise risks, avoid penalties, and gain a competitive advantage in the marketplace.
Unfortunately, in much of my experience, quality and assurance or regulatory and compliance officers and staff can often be seen as blockers in an organisation's speed to market and operations. A balance should be reached between more conservative approaches and delivery aims. Make sure you have an expert in the field advising early on in the ideation and development of the product; this will ensure an expedited process and a better product.
Pro Tip: Staying informed about regulatory changes by maintaining a proactive approach to compliance. Leveraging 3rd Party agents, advisors and testers can save time and money, allowing your business to focus on growth and product innovation.

Good practical advice - thank you